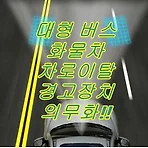
대형 사업용 버스, 화물차 차로이탈 경고장치 의무화 20년 1월부터 과태료 부과, 위반 횟수에 따라 3차 적발 시 150만 원 해외에서는 의무적으로 시행이 되는 곳이 많이지만, 우리나라는 이제 의무적 설치를 하게 하려고 합니다. 대형 차주님은 꼭 미리 설치하셔서 단속당하여 아까운 과태료를 납부하시지 마시기 바랍니다. □국토교통부(장관 김현미)는 버스, 화물차 등 대형 사업용 차량의 사고 예방을 위해서 차로이탈 경고장치(LDWS: Lane Departure Warning System) 미장 착자에 대해 내년 1월 1일부터 과태료를 부과한다고 밝혔다. * (대상) 사업용 차량인 9m 이상의 승합차 및 20톤 초과 화물·특수차 ㅇ차선이탈 경고장 치는 교통 안 전법상 의무적으로 설치하게 되어 있고 과태료 규정이..
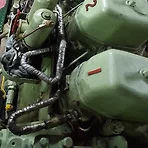
Here's a good data link to the ship's engine. 2019/04/10 - [자동차 & 선박 디젤 엔진 ] - INSTRUCTION MANUAL HEAVY DIESEL ENGINES!! 2019/04/18 - [자동차 & 선박 디젤 엔진 ] - Ship Engine Basic Configuration 2019/04/19 - [자동차 & 선박 디젤 엔진 ] - SHIP Turbo blower(TURBO CHARGER), Air cooler, Exhaust manifold This time, we will learn about ship engine Fuel Oil, ship engine Lubricating Oil, ship engine Cooling Water (Write a..
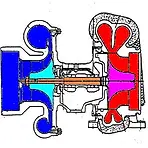
2019/04/10 - [자동차 & 선박 디젤 엔진 ] - INSTRUCTION MANUAL HEAVY DIESEL ENGINES!! INSTRUCTION MANUAL HEAVY DIESEL ENGINES!! Information sharing on diesel engines I am a Korean. Please understand even if I am not good at English. As I am interested in korea ship engines and korea car engines, I would like to share the inf.. ezexec2.tistory.com 2019/04/18 - [자동차 & 선박 디젤 엔진 ] - Ship Engine Basic Configura..
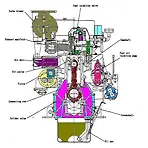
2019/04/10 - [자동차 & 선박 디젤 엔진 ] - INSTRUCTION MANUAL HEAVY DIESEL ENGINES!! INSTRUCTION MANUAL HEAVY DIESEL ENGINES!! Information sharing on diesel engines I am a Korean. Please understand even if I am not good at English. As I am interested in korea ship engines and korea car engines, I would like to share the inf.. ezexec2.tistory.com Ship Engine Basic Configuration The Diesel is designed as a ..
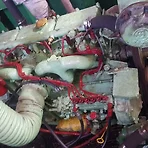
Information sharing on diesel engines I am a Korean. Please understand even if I am not good at English. As I am interested in korea ship engines and korea car engines, I would like to share the information I know about diesel engines. I am currently working on ship engines, and I have over 10 years of experience in handling and managing many engines, including mid- and low-speed diesel and YANM..
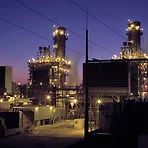
이번 시간을 마지막으로 기계, 생산, 제작 관련 단어 들을 정리 기계가공 용어 기계 용어 사전 기계공학 용어사전 가공 기호 등등 여러 단어가 중복으로 포함이 되어 있어서, 생산 직무 엔지니어에게는 도움이 될 것이고, 어느 생산 직무 엔지니어에게는 도움이 안 되는 단어도 포함이 되어 있을 것입니다. 필요한 단어, 용어만 찾으시면 될 거 같습니다. 저는 무에서 유를 창조하는 엔지니어 님들이 아티스트라고 생각합니다. 최고의 에이스 아티스트입니다. 그럼 많은 도움이 되시길 바랍니다. 이번 단어는 T에서 Z까지 준비되어 있습니다. 아래 참고 부탁드립니다. T toothed lock washer - 톱 니꼴 와셔 throttling calorimeter - 드로틀 열량계 two-dot chain line - 이점 ..
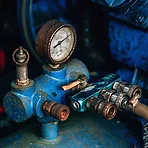
지난 시간에 이어 어려운 cnc 선반 교육 자료 제작 용어, 기계 단어, cnc mct 밀링 단어 등 기계나 제작을 하는데 토털 적으로 필요한 용어와 단어들을 수집한 자료입니다. 어떤 기술자에게는 필요 없는 단어 일수도 있고, 반대로 도움이 되는 교육 자료일 수도 있습니다. 기계를 다루면서 도움이 되었으면 합니다. 아래 단어들은 알파벳순으로 나열이 되어있습니다. 더 필요한 자료가 있으시면 언제든지 요청해주시면 최대한 도움을 드리도록 하겠습니다. 2019/04/02 - [자동차 & 선박 디젤 엔진 ] - 기계, 공학, 설계, 제작, 품질관리 단어/용어 공부해봅시다! (A~E) 2019/04/02 - [자동차 & 선박 디젤 엔진 ] - 기계 생산, 자동화 기계, 선반가공 기계 용어 모음입니다.(F~M) N ..
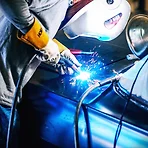
기계 생산, 자동화 기계, 선반가공 기계 용어 모음입니다. 저도 엔지니어이지만 용어를 모르면 많은 곤욕을 치르곤 합니다. 작업 시 그래도 도움이 되는 용어들을 모아봤습니다. 이번 시간에는 F~M까지 알파벳으로 시작하는 단어, 용어들을 모아봤습니다. 많은 엔지니어께서 개발, 가공, 제작, 생산, 설치하시는데 보탬이 되었으면 좋겠습니다. 저도 10년 차이지만 아직 많이 모르는 단어가 많습니다. 기계에 대해 지식과 경험이 있는 자동차 엔지니어, 기계 엔지니어, 비행기 엔지니어, 선박 엔지니어, 자동화 엔지니어 등 자기가 맡은 분야에 전문가가 되어 진정한 엔지니어가 되시기 바랍니다. F face plate - 면판(面板) forge fire - 화덕 firebox tube plate - 연소실 관 판(燃燒室管板..
- Total
- Today
- Yesterday
- 거버너
- 흡기
- 해양용어
- 디젤엔진
- 해양단어
- 조선단어
- 로또박사
- 속도조절
- 선박단어
- 흡배기
- 꿈해몽
- 해양플랜트
- 배기
- 로또당첨번호
- 조선
- 해양언어
- 선박부품
- 오늘운세
- 선박용어
- 꿈풀이
- bmw리콜
- 로또1등당첨지역
- 연금복권 당첨번호
- 의장
- 조선용어
- 해양조선
- 인물꿈
- 조선말
- 선박
- 엔진 정비
일 | 월 | 화 | 수 | 목 | 금 | 토 |
---|---|---|---|---|---|---|
1 | 2 | 3 | ||||
4 | 5 | 6 | 7 | 8 | 9 | 10 |
11 | 12 | 13 | 14 | 15 | 16 | 17 |
18 | 19 | 20 | 21 | 22 | 23 | 24 |
25 | 26 | 27 | 28 | 29 | 30 | 31 |